Material strength isn’t a
straightforward property, not when we’re talking about structurally-capable
alloys. Yes, a hardened work piece is stiff, but it could also be brittle. In
reality, strength is an amalgamated property, something that combines hardness
and material tempering. In using metal solidification technology as our
starting point, we’ll explain the importance of hardening, then we’ll introduce
tempering, a process that counters the hardening work by adding ductility to
the alloy amalgamation regime of Induction
Hardening in Faridabad.
Determining Central Precepts
The purpose of the hardening
stage is to ensure it won’t deform, no matter how heavy the applied load. If
that load compresses the metal part won’t collapse in upon it, won’t fracture,
nor warp. Instead, it stands resolute, with its original shape locked in place.
In essence, the mechanical backbone of the processed metal is stiffened. But
wait, a structure that’s imbued with this lone property could crack and
crumble, unless there’s a ductility feature in place, that is. Workpiece
tempering assumes this role, for this important low-temperature work phase is
purpose-built as a material brittleness alleviator.
Heat Treatment Balancing and Counterbalancing
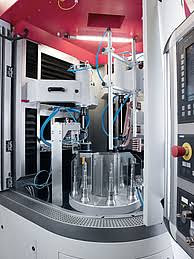
We’ve described quite a few hardening and tempering methods
over the months. They create tough metal parts and superior finishes, parts
that are as material strong as they are corrosion-resistant. Still, what we’re
stressing today is an overall strategy, a meeting of different heat treatment
principles and processes. Designed to produce a desired hardness-to-strength
ration, the hardening and tempering equipment use time and fiery temperatures
to imbue a chosen part with a requisite material strength rating in Induction Hardening.