What Is Induction Heating?

Induction Heating Applications
Induction
heating is used to manufacture end items as diverse as bulldozers, spacecraft,
faucets and sealing plastic lids on pharmaceutical bottles. The fundamental
design of an induction heating device uses a coil of wire and an AC current to
induce a changing magnetic field in the item to be heated—the work piece. The
coil can measure only a few centimeters in diameter, or any other dimension
suited to the job at hand.
The
work piece is placed inside the magnetic field generated by the coil, but not
in contact with it, then heated to the desired level by the eddy currents.
Depending upon the material being heated, temperatures as high as 2,200° F
(1,200° C) can be achieved.
Induction
heating is clean, requiring no fossil fuels. Parts exposed to induction heating
simply heat up, so there's no cleanup afterward and no worry about
contamination of the work piece. It's also fast. For example, manufacturers of
pipes and tubular channels use induction heating to weld a seam along the
longitudinal dimension of pipes passing by at high speed on a conveyor.
A
few other processes that use induction heating include:
- · Induction hardening and tempering, which alters the physical characteristics of materials to meet the needs of various applications.
- · Induction melting can be used to melt any ferrous or non-ferrous metal, including nuclear material and various alloys used in medicine and dentistry.
- · Metal and carbon fiber materials can be bonded together by heating them, thereby curing adhesives placed between two surfaces.
- · Soldering, brazing and welding are all natural applications for induction heating where precise temperature control and accurately confining heat to the desired area is important in air cooler oil cooler.
Induction
Heating Solves Real Problems
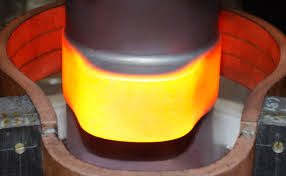
The
aluminum foil that's commonly used to seal OTC drugs is part of the industry's
solution, and it uses induction heating. The process begins by placing the
foil, which is electrically conductive, into the cap. The cap is screwed down, and
then the entire package is placed inside an induction heating coil. As the foil
heats up, adhesives around its edge adhere it to the lip of the bottle.
Designers
of induction cap sealing equipment must take several factors into account. The
induction heater's physical dimensions need to be tailored to the containers to
be sealed. The electromagnetic field needs a depth suitable for heating the
foil. The heating should take place as quickly as possible for productivity
reasons. The efficiency of the induction heater needs to achieve a specific
performance level.
These
and other design constraints can be reduced dramatically when the wire used to
make the coil is custom-manufactured. New England Wire Technology, a long-time
supplier to the induction heating market, provides wire specially made to solve
such design problems in Induction Hardening
Faridabad.
For
instance, NEWT can supply round, square and rectangular conductors. Their exact
size can be tailored specifically for the AC current and frequency to be used.
And, because the efficiency can be optimized in the wire itself, the induction
cap sealer design engineer has much greater flexibility in choosing the
spacing, shape and size of the sealing head. In fact, that same flexibility
benefits designers of any induction heating device.
Case Hardening
Heat-treatment processes
such as case hardening are used to prolong the service life by increasing the
surface hardness and vibration resistance while maintaining a ductile, elastic
microstructure at the core. Steels suitable for case hardening have a carbon
content of approximately 0.1-0.3% weight percent. For a high surface hardness –
for example, 60 HRC – a carbon content of 0.1-0.3% is not sufficient. The part
has to be carburized.
Carburization takes
place by diffusion of the carbon into the work piece surface. A mixture of
carrier gas and additive gas forms the basis for the carburization atmosphere
in the furnace. Crucial factors for the right choice of the carburization
process are the material-specific parameters, hardening demands in conjunction
with the gas composition and a continuous, homogeneous furnace atmosphere.
Hardening is achieved by
heating to austenitizing temperature with a sufficiently long holding time and
subsequent quenching process. What is crucial here is that the carbon in the
austenite is brought into solution. The amount of carbon is dependent on the
material composition and the state of the initial microstructure. Excessive
holding times or excessive temperatures during the austenitizing process can
have a negative impact on the grain growth and material microstructure.
The hardening process
can be followed by a low-temperature cooling process or direct tempering
process. Both processes result in a reduction of the residual austenite and of
the hardness and distortion properties.
Tempering is performed
in different temperature ranges. The tempering temperature of parts made of
low-alloy or unalloyed steels generally lie between 180-250°C (356-482°F). A
higher temperature leads to a greater drop in hardness.
No comments:
Post a Comment